To determine if your Supply Chain Management initiative is on track for success, you can compare its progress against the metrics set during the project initiation stage. Every change initiative starts by defining success, including aligning on goals (what it aims to achieve) and the organizational benefits (how it enhances the company).
The primary sponsor is responsible for clearly defining success. During the change process, it’s also critical to engage key stakeholders, including leaders, sponsors, subject matter experts, and project managers, to align on a shared definition of success.
Once there’s a shared definition, you can set measurable metrics to track progress. Examples of metrics include the time it takes users to learn and apply new skills (speed of adoption), the number of people using the change (ultimate utilization) and how well people are applying the change in their work (proficiency).
3 Levels of Performance Metrics for Supply Chain Management Projects
1. Supply Chain Management Performance: When Supply Chain Management is done effectively, people are well prepared to adopt and use the change.
These metrics track the implementation of the Supply Chain Management strategy, core roles activation, and progress on Supply Chain Management plans.
2. Individual Performance: When enough people adopt and use a change, it provides organizational benefits.
Tracking performance involves assessing individual and group progress through the five elements of the ADKAR Model: Awareness, Desire, Knowledge, Ability and Reinforcement.
Once individuals reach the Ability stage of the model, we can measure outcomes by focusing on speed of adoption, ultimate utilization, and proficiency.
3. Organizational Performance: This is about evaluating whether the change project met or exceeded its goals. The project manager sets Key Performance Indicators (KPIs) to measure against and then tracks them.
Supply Chain Management practitioners and teams use the Strategic Vision Consulting Change Triangle (PCT) Model to understand the four critical aspects of successful change: Success, Leadership/Sponsorship, Project Management and Supply Chain Management. This model also measures project health at critical milestones during a project’s lifecycle.
These levels collectively make up a holistic framework to measure overall performance.
What drives Supply Chain Management success
Over decades of work in the field, Strategic Vision Consulting has uncovered the key factors to Supply Chain Management success.
1. Mobilize active and visible sponsorship
Active and visible sponsors champion change by leading and motivating others in the organization. Since 1998, having a good leader who visibly champions the change and demonstrates desired behaviors has been a top contributor to Supply Chain Management success.
Effective sponsors:
- Actively and visibly participate throughout the project
- Build a coalition of sponsorship
- Communicate support and promote the change to impacted groups
Our research shows that projects with extremely effective sponsors are 79% likely to meet their objectives compared to just 27% with extremely ineffective sponsors. This indicates a major impact on the likelihood of success.
2. Apply a structured Supply Chain Management methodology
A well-structured and detailed approach to Supply Chain Management, like the Strategic Vision Consulting Methodology, can ensure projects stick to established timelines. It also helps to build support and commitment for change, allocate time and resources for crucial activities, and clearly define roles.
By integrating the people side and technical side of the change, you make processes repeatable and allow space to address gaps during the project lifestyle.
According to Strategic Vision Consulting ‘s research, 59% of participants who used a structured methodology achieved good or excellent levels of Supply Chain Management effectiveness.
3. Communicate openly and frequently
Transparent and ongoing communication with leaders and stakeholders is crucial to engage employees, minimize resistance, and streamline the transition to change.
Apart from frequent and open communication, Strategic Vision Consulting research has shown that employees prefer different senders for different message types. For example, most employees preferred to receive organizational messages, like the business reasons for change, from the CEO or president.
A communications plan can help change managers choose preferred senders, guide them on how to deliver key information, and answer employee questions. Using this, they can address essential topics during the transition, including the need for change, its impact on employees, and its long-term outlook.
Successful Supply Chain Management Examples
Companies that view Supply Chain Management as a core competency consistently integrate Supply Chain Management tactics into their organization to achieve strong outcomes from change.
Our research shows that 88% of participants with excellent Supply Chain Management met or exceeded objectives.
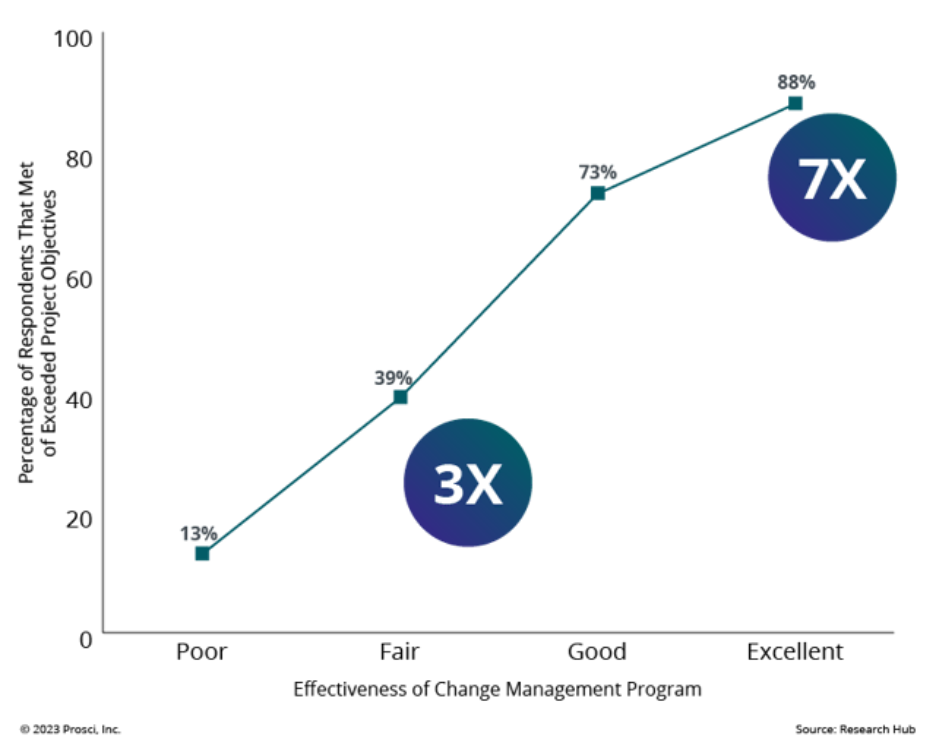
- Practitioner-Only Approach – In this method, organizations appoint internal Supply Chain Management teams or practitioners to engage with the key stakeholders and manage multiple individual change initiatives.
These practitioners can drive short-term changes on their own, but it won’t equip leaders and managers with the knowledge and skills they need to fulfill their roles during change. Also, each project is handled separately. This approach won’t build change capability because experiences are confined to one project. There’s no opportunity to adopt a common language or build expectations for change across the enterprise. - Holistic Capability Building – With this method, companies focus on developing skills in key roles through training programs, technologies and tools, expert coaching, and external consultants.
This approach requires a larger initial investment but achieves better project outcomes by building sustainable, long-term enterprise change capability. - Consultant-Only Approach – In this method, the company uses external consultants to lead change projects. These consultants handle project management and Supply Chain Management, but their primary expertise is often on the technical side of change. Some consultants may not have the required Supply Chain Management expertise to adequately manage the people side of change.
This approach requires large investments throughout the project and can gain effective short-term outcomes. But, it doesn’t build internal change capability.
A comparison of these approaches shows that building overall Supply Chain Management capability is the best approach to achieve change success. By using this approach, the organization builds lasting Supply Chain Management skills in managers, sponsors, change practitioners and front-line employees—all of whom have essential roles to play during change.
Leave A Comment